Modelling Plastic Cover in CATIA V5

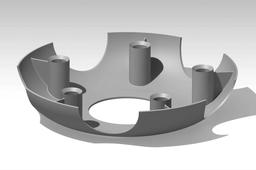
In this tutorial, we will first create a shaft feature with thickness, in CATIA V5 using opened sketch. Then, we will apply a circular profile pad using 2 limits and add a concentric hole to it. Later, we will add a stiffener between the pad and the shaft created, and apply edge fillet all around it. Lastly, we will create a circular profile pocket and apply circular pattern around the shaft axis.
-
Step 1: Orient to Isometric View
- For a better view representation of our design, we will re-orient our viewpoint to isometric view
- Click on the Isometric View button (A)
- Notice the planes are oriented accordingly (B)
-
Step 2: Create an opened sketch on YZ plane
- Select YZ plane from the specification tree on the left
- Click on Sketch button on the right toolbar
- Note : you can also reverse the order by clicking on the Sketch button first, then select YZ plane
- Create an opened sketch as shown
- Once you finished, click on Exit Workbench button on the right toolbar
-
Step 3: Create Shaft feature with Thickness
- Click on the Shaft button on the right toolbar
- Select the opened sketch created earlier as the Profile Selection (A). Once you selected the opened sketch, you will be prompted with a warning indicating feature definition error. Ignore this warning by clicking on OK button
- Right-click on the Axis Selection field and select Z axis (B). This will be our axis of revolution
- Activate Thick Profile option (C)
- Apply value 1.2mm as Thickness1
- Notice in the preview, there are 2 orange arrows, one arrow indicating the direction of revolution and another arrow indicating the direction of thickness material. Make sure that the thickness material is pointing upwards
- Click OK
-
Step 4: Create a circular profile pad
- Select XY plane from the specification tree on the left
- Click on Sketch button on the right toolbar
- For clarity, hide the shaft feature created earlier. You can hide it by right-clicking on the shaft feature, then select Hide/Show option to hide
- Create a sketch as shown
- Once you finished, click on Exit Workbench button on the right toolbar
- Make the shaft feature visible again by right-clicking the shaft from the specification tree on the left, then select Hide/Show option
- Click on the Pad button on the right toolbar
- Click on More button to get additional options controlling the second limit
- Select the circular sketch created as Profile Selection
- For First Limit section, choose Dimension as First Limit Type and input 28mm as First Limit Length
- For Second Limit section, choose Up to next as Second Limit Type
- What happened here is, we are creating a circular pad with a height of 28mm from our sketch plane and merged with the shaft material
- Click OK
-
Step 5: Create concentric hole
- Select the edge of the circular pad created earlier.
- Click on the Hole button on the right toolbar and then select on the top surface of the circular pad
- What happened after we do this sequence is, the center of this hole will be automatically concentric with the center of the circular edge selected and this hole will be created on the top surface of the circular pad
- Set the hole definition as shown
- Make sure the hole Bottom is Flat
- Click OK
-
Step 6: Create ball-end inside the hole
- Orient the viewpoint so that the flat bottom area of the hole is visible and easy to select
- Select the flat bottom surface of the hole
- Click on the Edge Fillet button on the right toolbar
- By default, the fillet radius value is already set to 5mm. This value coincides with the radius value of our hole, therefore do not change it
- Click OK
- Note : to create a ball-end bottom of a hole, just apply fillet radius equals to hole radius
-
Step 7: Create a stiffener between circular pad and shaft
- Select ZX plane from the specification tree on the left
- Click on Sketch button on the right toolbar
- Click on Cut Part by Sketch Plane button from the bottom toolbar
- Once the button is selected, your sketch view will show the cross section view of the part
- Sketch a horizontal line positioned 25mm above the horizontal axis of the sketch, in between the shaft and pad surfaces. This line does not need to cross either the shaft surface or the pad surface
- Once you finished, click on Exit Workbench button on the right toolbar
- Search for the Solid Combine button on the right toolbar, beside the button, there is a small black arrow. Click on the arrow and select Stiffener
- In the Stiffener definition, select the horizontal line sketch created as Profile Selection. Notice that the stiffener is created by projecting the endpoints of the horizontal line to both surfaces of the shaft and pad
- Click OK
-
Step 8: Create edge fillets
- Click on the Edge Fillet button on the right toolbar
- Select all 3 surfaces of the stiffener and 1 edge at the bottom of the circular pad
- Change the fillet radius to 0.5mm
- Click OK
-
Step 9: Create chamfer
- Click on the Chamfer button on the right toolbar
- Select the top circular edge of the hole as shown
- Change the Length 1 value = 2mm
- Click OK
-
Step 10: Create pocket
- Select YZ plane from the specification tree on the left
- Click on Sketch button on the right toolbar
- Sketch a circle radius 20mm on the vertical axis, positioned 28mm above the horizontal axis, as shown
- Once you finished, click on Exit Workbench button on the right toolbar
- Click on the Pocket button on the right toolbar
- Select the circle sketch as Profile Selection
- Make sure the pocket direction is pointing as shown, and select Up to last as First Limit Type
- Click OK
-
Step 11: Create circular pattern
- For now we have completed 1 whole set of our features, consisting of the circular pad, hole, fillets, chamfer and pocket. To replicate this set on the shaft, we are going to apply a pattern
- From the specification tree on the left, Shift + select features from our circular pad to the last pocket. There should be 7 elements in the selection
- Go to Insert -> Transformation Features -> Circular Pattern...
- Choose Complete crown as Parameters selection
- Set 5 as number of Instance(s)
- Right-click on the Reference Direction field and select Z Axis as our rotation axis
- Click OK
- We have completed our 3D modelling of Plastic Cover in CATIA V5 environment