PolyJet Multi-Color Design Guidelines for 3D Printing

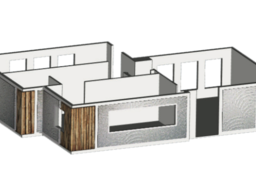
PolyJet Multi-Color builds prototypes, models and other parts in full color, including gradients and graphic textures. These design guidelines provide instructions for specific design considerations, including file exporting procedures and color selection for multi-color parts.
-
Step 1: File Formats & Design Considerations
There are two file formats utilized for multi-color PolyJet parts: STL or VRML. Use of either option depends on the part’s color and transparency needs. The file formats assign color and texture graphics to parts in unique ways.
It is important to look at the specifications for each design consideration.
-
Step 2: STL
Shell-based format (STL) is used when a colored model requires the use of a clear material or color tinted transparencies, such as with medical models that utilize clear material to show interior anatomical features or a colored display unit with a clear window. Color and transparency are assigned within the assembly with a RGD color code from the PolyJet Color Guide.
If the 3D model of the part is separated into shells (different parts combined together into one assembly), designers can choose the colors and level of transparency of each shell. This is also indicated with the PolyJet Color Guide RGD color code and/or checkered pattern which indicates transparency.
With an assembly that is built as one part, multiple sections of the assembly will be the same color code and submitted as a single STL. For example, someone may design a clear square with yellow lettering on the interior, such as a company’s logo and name. The letters are not connected to each other, but since they are part of the assembly, held together by the clear square, every letter will be saved as a single STL. The designer will save a lot of time because they won’t have to assign individual color codes.
A boolean tool is recommended using third-party STL manipulation software for designers using STL format. The tool adds, subtracts and intersects space between two objects. If the boolean option is not used, there is a potential that overlapping parts could be assigned a random color by the PolyJet technology, and areas with space between walls may generate supports and could separate during handling.
Stratasys Direct Manufacturing project engineering staff will append the file names of STL files to include the color code assigned. Customers can either submit a document outlining what color code goes with each STL in the assembly, or label each STL within assemblies with the RGD color code.
-
Step 3: VRML
Virtual Reality Modeling Language (VRML) format is ideal for parts designed with opaque colors or a colored graphic texture. VRML (.wrl) is a standard file format for representing 3D interactive graphics that provides the capability to apply texture to a model. VeroClearTM material or translucent colors cannot be used in this format.
The use of VRML files is much easier when dealing with multiple colors. Depending how color is applied, the color could be within the VRML file itself, or the VRML file could be accompanied by one or more texture files (.bmp,.jpg, .tiff, .png). Possible uses for this process include FEA parts that show a colored depiction of heat or stress or a prototype when the graphics on the product are complex, such as a shampoo bottle with multiple colors, logo/brands, etc.
Color can be applied in VRML format to each face of the geometry, to each individual triangle or with a graphic texture file.
Color per Object, Mesh or Shell
When designing a model in CAD, each part is assigned with a solid color (usually referred to as diffuse color or material color).
Color Per Face
A square face is made of two triangles. Designers can color the entire face or can color the individual triangles two different colors. A face can be anything from one triangle in a mesh to as many polygons as selected.
Color Per Vertex
Each vertex of every triangle has a color value and the color is interpolated across the mesh. The quality of the color is related to the resolution of the model.
When designing a model with colors (not textures) and saving the colors per object, face or vertex, all the data regarding the color is stored in the .wrl file.
-
Step 4: Color by Texture / UV Mapping
Texture mapping, also known as UV mapping, is the process of adding an image or graphics to 3D geometry. Color information is stored in a 2D image file, which is related to the coordinates of the mesh. This type of file can show the most detailed color information.
Designers can use specialized third-party software to “unwrap” the 3D mesh into a 2D space. These programs allow designers to add color and detail from images that will later be wrapped back into the model. When applying a texture to a model with any software, a file with the texture is generated. The model geometry is “wrapped” with the texture in a process called UV mapping. For good print resolution, the image file should be 600 DPI and the UV mapping size must match the model size.