POLYJET SUPPORT MATERIALS PART 2: SUP705 & SUP706B

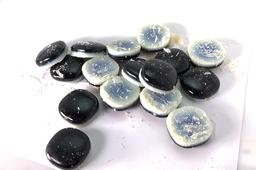
Learn the best 3D printing workflow for PolyJet support material SUP705 and SUP706B, including pre-printing design tips for easier support removal to post processing tips.
-
Step 1: Overview
In a previous tutorial about Support material for PolyJet, we introduced the 3 PolyJet Support materials, SUP705, SUP706B, and SUP707, and provided a summary of each material’s properties and characteristics. In this tutorial, we will provide the workflow for SUP705 and SUP706B, from pre-printing design tips for easier Support removal to printer preparation and GrabCAD Print setting recommendations to post processing.
-
Step 2: Advanced Design- Pre-Printing Tips for Easier Support Removal
There are a few ways to optimize model design for easier support removal after printing:
1. Enclosed Hollows
For any hollow parts that are long and/or narrow, nest a second, smaller, identical, solid shape inside After printing, simply remove the nested part.
2. Moving Part Assemblies
Create slots or openings in rotating assemblies to help remove support material
3. Tubes
For long, hollow tubes, it might be helpful to use a removable sacrificial rod.
4. Deep voids and enclosed sections
If possible, design deep voids with exit holes. This will speed up post processing and final part finish.
This is especially important for moveable sections and clear parts, as Support material remnants would compromise their appearance and tolerance.
-
Step 3: Preparing the printer and GrabCAD Print
1. Load the Support cartridge(s).
2. If you’re switching between support materials:
a) Run the Material Replacement wizard.
b) Run the Head Optimization wizard.
3. Optimize GrabCAD Print settings
The default grid style used for SUP706B is Lite Grid. Change the grid style to Heavy Grid—
- when printing with Tango materials.
- when the model includes floating parts that are more than 30 mm high.
-
Step 4: Support removal and post processing
SUP705 and SUP706B follow roughly the same Support removal process. The biggest difference is that SUP705 relies mainly on a WaterJet for final removal, while SUP706B can also be placed in a cleaning station instead of or in addition to a WaterJet.
Therefore, SUP706B provides a Support removal process that can be:
· Easier, more efficient, and in some cases faster
· Streamlined for large quantities of parts
· Viable for parts that are delicate, finely detailed, or built with complex geometries like inner channels.
Below is the process for removing SUP705 and SUP706B.
1. Break away as much excess Support material as you can by hand.
Wear protective gloves. Removing whatever can be easily removed before using the solution bath extends the effectiveness of the solution and saves time and money, as the solution bath will not get saturated as quickly. It will also help prevent delicate models getting damaged or broken by excessive soaking or WaterJet use.
For delicate models, use a toothpick, pin or small brush after dipping the model in water.
Optional: before breakaway, if you have a large volume of parts, you can soak them in plain, room temperature water or in a solution of water and dish detergent for 1-2 hours. This will help loosen up the support material. Do not use warm water as PolyJet parts can soften and warp in heat
2. Soak the model in a caustic soda solution to remove Support material from difficult-to-reach areas and to give the model a smooth, clean finish.
Soak for half an hour to several hours, depending on how delicate the model is and how much Support material needs to be removed. Models with walls less than 1 mm thick may deform slightly if soaked for more than one hour. The more parts you soak at once, the longer it will take.
· For SUP705, use a 1% caustic soda solution (sodium hydroxide)
· For SUP706B, use a 2% caustic soda and sodium metasilicate solution
3. Remove the remaining Support material:
· If you print with SUP705, Rinse the model thoroughly with a WaterJet. Take care with delicate models.
· If you print with SUP706B, you can use a cleaning station. Place models in a suitable cleaning tank containing a solution of 2% sodium hydroxide and 1% sodium metasilicate (Na2SiO3). The cleaning tank should employ a pump (or other device) that circulates the solution continuously.
4. For SUP706B, rinse models in running water and gently rub the surfaces to prevent a white layer from forming on the surface.
5. Optional: To strengthen models and optimize surface quality, dip them in a 15% glycerol solution for 30-60 seconds, then place them on a mat to dry. We recommend a technical-grade glycerol with 97% purity level. Do not wipe or wash models after dipping in glycerol. In some cases, prolonged model soaking in alkaline solution may adversely affect the mechanical properties of the model.
These steps are geared for general-purpose Support materials for models, for most printing applications. Use this information as a guide, and adapt the methods (or a combination of them) for cleaning your models.
For special printing applications, including Digital Anatomy models, refer to Support removal instructions on the Stratasys Support Center or consult a Stratasys 3D printing expert.
Not sure whether you should use a WaterJet or a cleaning station? Use our infographic:
-
Step 5: Conclusion
This concludes our series on Support materials.
You can also check out these previous tutorials about removing SUP706B or our intro to PolyJet Support material. Or you can read about SUP706B in our Stratasys Support Center.
Have any other questions or comments about Support material for PolyJet? Leave a comment below.