How to calibrate Fortus 360MC & Fortus 400MC systems

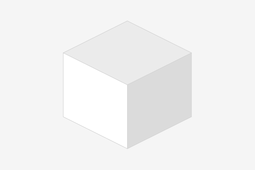
Process
-
Step 1:
Step 1: Install a clean plastic sheet and allow vacuum pressure to reach -15 Hg or greater.
-
Step 2:
Step 2: Go into the Calibrate menu and run Auto Z Stage Zero Calibration. If this calibration fails, follow Steps 2a through 2i to set the Z Zero with Shim.
-
Step 3:
2a From the main menu on the keypad select Operator Control and press enter.
-
Step 4:
2b Select Calibrate and press enter.
-
Step 5:
2c Select Set Z Stage Zero and press enter
-
Step 6:
2d Select Set Z Zero with Shim and press enter. The Z stage moves into position and the head moves out.
-
Step 7:
2e Open the oven door and insert the door bypass tool supplied in the start up kit.
-
Step 8:
Note: There are different types of “cheater” tools for 360mc and 400mc systems
-
Step 9:
2f Insert the shim between the tip and the build sheet. The shim is the piece of thin metal included in the start-up kit.
-
Step 10:
2g Manually raise the platen using the #3 key on the keypad until the tip just touches the metal on the shim and you can feel a little resistance. The Z stage movement increment can be changed by toggling through the selections on the Set Distance = line
-
Step 11:
2h Press enter at the Set Z Stage = 0 cursor on the keypad. The Z coordinate is read and stored, then the table moves down one inch and the head goes
to the park location. Make sure you don’t remove the cheater or open the hood until the table stops moving. -
Step 12:
2i Remove the shim and door cheater.
-
Step 13:
STEP 3: Under the Calibrate menu, select the AutoCal Tips operation.
This operation will take a few minutes to complete. -
Step 14:
STEP 4: Next run a Cal Job. (For best results, run Cal Job as close to
the center of the platen as possible.) -
Step 15:
STEP 5: Inspect the calibration job and make any necessary adjustments according to steps 5a through 5g below.
-
Step 16:
5a Remove the build sheet from the platen and allow it to cool.
-
Step 17:
5b Hold the build sheet up to a light, a light-colored wall, or a light-colored piece of paper and, using a magnifier, view the relationship between the Support Calibration Toolpath and the Alignment Indicators to determine the X
and Y Axis calibration. On a correctly calibrated machine, the Support Calibration Toolpath will be centered between the two Alignment Indicators next to the “zeroes” on each axis. -
Step 18:
5c If the Support Calibration Toolpath is not centered between any of the zero indicators, determine where on each axis the support is the most centered, and then enter the corresponding adjustment under Operator Control/Calibration/Tip Offset Value on the Control Panel. (For example: If the support is most centered between the indicators below the “4” on the top side of the calibration box, you would enter “.004” into the “-Y” Tip Offset Value line.)
-
Step 19:
5d Run another Cal Job and verify proper calibration, or make additional adjustments and repeat.
-
Step 20:
5e Once you have the X and Y calibration adjusted properly, you will then peel the support layer from the Z Calibration box in the center and, using a caliper or micrometer, measure the thickness of the support layer.
Note
Do not attempt to check the Z-height until you are sure
that the X and Y calibration are correct! If the Z-height
toolpath is not centered on the model material below it,
you will not get an accurate measurement. -
Step 21:
5f This support layer should measure within +/- .0005” of the slice / layer thickness that corresponds to the model tip installed in the machine (T16 tip = .010”, T12 = .007”, and T10 = .005”). If the Z-height does not meet this specification, adjust accordingly using the “+Z” or “–Z” lines in the Operator Control/ Calibration/Tip Offset Value area on the Control Panel.
-
Step 22:
5g Run another Cal Job and verify proper calibration, or make additional adjustments and repeat.