How To Properly Sterilize FDM Parts

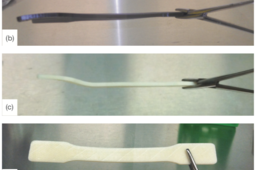
Fused Deposition Modeling (FDM) is an additive manufacturing technology that is used in industry for development of three-dimensional models. Because of its ability to provide highly accurate models, FDM may offer many benefits to those wishing to use it for a range of medical applications. FDM can be used to build models that aid physicians in the surgical planning process or in the production of a surgical implant. It can be used to achieve a patient’s agreement prior to surgery by providing a preoperative simulation device. During surgery, an FDM model can act as an orienting aid or a template for resection. FDM can also be used to directly manufacture medical implants out of bioimplantable materials. However, such surgical devices and implants will come into direct contact with sterile body tissues and fluids, and therefore, must be manufactured out of sterilizable materials.
-
Step 1: Creating an FDM Part
Construction of an FDM model is a multi-step process.
Step A: A computer-aided design is made and is exported in “.stl” format. Models can also come from computed tomography scans, magnetic resonance imaging, or ultrasound.
Step B: The design is then processed by either Insight® (Stratasys), the software used to set the desired build parameters, or GrabCAD Print.
Step C: Once these have been established, the file is downloaded by the FDM system.
Step D: A spool of solid material is fed into an extrusion head which heats it to a semi-liquid state. The head deposits the semi-liquid material one layer at a time. Because the temperature inside the envelope – the chamber in which the model is built – is lower than the material’s melting temperature, the layers solidify as they are deposited. If necessary, the head can extrude a support material that can later be removed, to hold the layers in place as they cool.
-
Step 2: FDM Materials
The materials commercially available for use in FDM are thermoplastic polymers. Acrylonitrile butadiene styrene (ABS) is a commonly used material for construction in FDM.
ABS derivatives include: ABSi, ABS-M30, ABS-M30i, ABS-ESD7, and PC-ABS.
ABSi’s translucent nature allows it to be used when monitoring material flow or transmission of light. This material is used mostly in the automotive industry.
ABS-M30 is considered stronger than standard ABS. This makes the material ideal for achieving more realistic results in functional tests and higher quality end-use parts.
ABS-M30i is biocompatible as per ISO 10993 USP Class VI. This makes it a good candidate for use in the medical, pharmaceutical, and food packaging industries.
ABS-ESD7 has static dissipative properties which allow the material to be used in applications where products may be damaged as a result of static charge. This also prevents powders, dust, and fine particles from sticking to it. Because of this, it is used mostly in the assembly of electronic components.
PC-ABS is a polycarbonate-ABS blend. It is widely used because it offers the strength and heat resistance of PC as well as the flexibility of ABS. It is also used in the automotive, electronics, and telecommunications industries.
Other FDM materials are PC, PC-ISO, PPSF and ULTEMTM 9085 thermoplastic resin.
PC is considered a true industrial thermoplastic due to its accuracy, durability, and stability in creating parts for functional testing. It is widely used in automotive, aerospace, and medical applications.
PC-ISO, in its raw state, is also biocompatible as per ISO 10993 USP Class VI. It is, therefore, commonly used for food and drug packaging as well as medical device manufacturing.
PPSF, or polyphenylsulfone, has the greatest heat and chemical resistance of all FDM materials. Parts built of this material are not only mechanically superior but also dimensionally accurate. It is an ideal material for use in aerospace, automotive, and medical applications.
ULTEM 9085 is a flame retardant high performance thermoplastic resin. It can be used in the commercial transportation industry, especially in the manufacturing of aerospace, marine, and ground vehicles.
Using the nine FDM materials described above, this tutorial describes sterilization testing on these materials using four methods of sterilization (autoclave, ethylene oxide gas, hydrogen peroxide gas plasma, and gamma radiation) that will be more fully described in the following steps.
-
Step 3: Sterilization Materials and Methods
Sample Construction
The ASTM D638 Type I was selected as the shape of choice for the samples used in these tests. These samples had a length of 165.1 mm, a maximum width of 19.05 mm, and a height of 3.175 mm . They were manufactured on a Fortus 400mc 3D Production System. Build parameters were set using Insight 8.1: raster width at 0.508 mm, raster angle at 45°, contour width at 0.508 mm, and slice height at 0.254 mm. A T16 tip was used for the model material while a T12 was used for the support. The samples were built at the flattest orientation, with the height along the Z-axis at 3.175 mm. Thirty samples were built of each of the nine FDM materials: ABSi, ABS-M30, ABS-M30i, ABS-ESD7, PC-ABS, PC, PC-ISO, PPSF, and ULTEM 9085 thermoplastic resin. Five test samples and one control were used for each method of sterilization.
Autoclave
The samples were autoclaved using a SANYO Labo Autoclave MLS-3750. This equipment allows the user to establish the temperature and duration of the cycle. The pressure is a consequence of these two settings. Two different cycles were tested for this procedure; five samples of each material per cycle.
The first cycle was set at 121°C for 20 minutes. These samples were packaged according to material type in autoclavable bags (5 samples per bag). The maximum pressure reached in this cycle was 0.20 MPa.
The second cycle was set at 132°C for 4 minutes. This cycle reached a maximum pressure of 0.12 MPa. This cycle is known as a “flash autoclave” cycle because it is faster. These samples were individually packaged in self-seal sterilization pouches. Both cycles had heating and pressurization as well as cooling and depressurization periods that were approximately 30 minutes long.
Ethylene Oxide Gas
Five samples of each material were sterilized by ethylene oxide in an Anprolene AN74i sterilizer. Two cycles are available for this procedure: 12-hour and 24-hour.
The 12-hour cycle was selected knowing that if this cycle failed, the 24- hour could be tested as well. These samples were individually packaged in self-seal sterilization pouches.
Hydrogen Peroxide Gas Plasma
The third method of sterilization, hydrogen peroxide gas plasma, was done using a STERRAD 100S sterilization machine. Again, five samples of each material were used. The cycle duration was 55 minutes at a maximum temperature of 55°C. The cycle time is dependent on the type of STERRAD machine that is used. The 100S has only one cycle setting and changes cannot be made. This procedure was conducted at a different facility. The samples were individually wrapped in Tyvek pouches so that they would remain sterile during transportation. Such pouches are permeable to hydrogen peroxide.
Gamma Radiation
The last set of samples was submitted to the fourth and final method of sterilization, gamma radiation. This was conducted in a JS8900 Batch Gamma Irradiator by STERIS: Isomedix Services. The samples were also individually wrapped in self-seal sterilization pouches and shipped in a cardboard box with dimensions 323 x 279 x 45 mm. Once received by the processing center, the samples were not removed from their packaging and were sterilized within the box. The radiation dosage was approximately between 25 to 35 kGy. However, this is not a guaranteed dosage as the samples were submitted as a research run and no certificates of processing were provided.
Sterility Test
The sterility test – performed to confirm the success of each sterilization process – was designed based on guidelines obtained from the U.S. Food and Drug Administration (FDA) and Daniëlle Neut’s paper, “A Gentamicin-Releasing Coating for Cementless Hip Prostheses- Longitudinal Evaluation of Efficacy Using In Vitro Bio-Optical Imaging and its Wide-Spectrum Antibacterial Efficacy.” BactoTM Tryptic Soy Broth (TSB) was prepared and sterilized via autoclave at 121°C for 20 minutes. Once the test samples were sterilized by the corresponding method, the test was used to determine the success or failure of the sterilization process.
The control samples were treated to the same incubation procedure. However, prior to incubation, these did not undergo any type of sterilization.
-
Step 4: Results of Sterilization
Prior to use, TSB is a transparent liquid. If the TSB is exposed to a microbial or fungal agent, the organism will reproduce, making the liquid turbid. Precipitation can accumulate at the bottom of the vessel if enough of the organism has settled. Turbidity and precipitation are indicators that the sterilization was not successful.
Samples showing these characteristics are represented by a (+) sign in Table 1. No turbidity or precipitation in the TSB indicates there are no organisms present; therefore, sterilization was successful. These samples are represented by a (-) sign in Table 1. All but one of the control samples (ABS-ESD7, flash autoclave) yielded positive results.
None of the samples were purposefully contaminated prior to testing. This means that any contamination seen on the samples may have been acquired during the manufacturing and transportation processes as these were conducted in a non-sterile way. Because all but one control showed positive contamination, any non-sterile test samples should also show contamination.
Flash autoclave, hydrogen peroxide gas plasma, and gamma radiation were all 100% successful in sterilizing the test samples. The TSB remained clear because no contaminants were present in these tubes.
A few test samples did, however, show contaminants. During the autoclave testing, one of five ABS-M30 samples was turbid. Two of the ABS-M30i samples were turbid as well. Of the samples sterilized with ETO, only one of five ABS-M30 samples was turbid.
Because the occurrence of a positive result was so rare, it is possible these samples were contaminated following sterilization as they were being prepared for incubation. It is important to note, though, that contamination of ABS-M30 occurred for two sterilization methods.
Although a large majority of the test samples showed they could successfully be sterilized by each of the methods, not all of them withstood the sterilization procedures themselves (Table 2).
All 9 materials seemed unchanged after sterilization by ethylene oxide gas, hydrogen peroxide gas plasma, and gamma radiation. However, the high heat and moisture of the autoclave caused damage to some of the materials. For example, after the first autoclave cycle, bending and indentations were seen in ABSi, ABSESD7, ABS-M30, ABS-M30i, and PC-ABS, all of which are ABS derivatives.
The indentations were caused by the metal basket used to hold the samples in the autoclave chamber. Some of the samples were also attached to one another as if melded together by the heat. For this reason, the samples were packaged individually for the flash autoclave cycle. However, the flash autoclave cycle also damaged all of the ABS derivatives. Bending was very apparent as well as indentation. Although some of the indentation was from the holding basket, there was also some that appeared to be a result of the moisture retained by the bags post-sterilization. Color change was also noted. Slight bending of the samples was also seen in PC as a result of the flash autoclave cycle.
-
Step 5: Conclusion
FDM is a technique that is useful in a variety of applications, including some medical ones.
The spectrum of medical applications can be expanded to include surgical tools or devices where direct contact with the patient is made. This can only be achieved if the FDM materials used to build such devices are deemed sterilizable. Based on this tutorial, it appears that each of the four methods tested are successful in sterilizing these materials. However, it is clear that ABS derived materials cannot resist the high temperatures of the autoclave. Although the autoclave is most likely the simplest sterilization method available, it is best to use more heat resistant materials, such as PC-ISO, PPSF, or ULTEM 9085 thermoplastic resin when using high temperature sterilization methods.